Michael Bower has a vision for Eagle Metalcraft, and that involves investing more than $1 million in capital investments in a three-phase project this year.
“We are making this capital investment to add capacity,” Michael said. “Our number one challenge is finding skilled trade team members that fit and contribute to our culture. The only way to stay competitive is by investing in modern equipment and improving floor and flow layout through lean initiatives.”
On May 4, Eagle Metalcraft launched phase one of our three-phase Capital Project, which included reorganizing the floor layout to improve manufacturing efficiencies and preparing for the arrival of new equipment in Phase 2. We also began replacing areas of our work floor to better support the new equipment, including last week’s delivery of the New Haas 4FV SS.
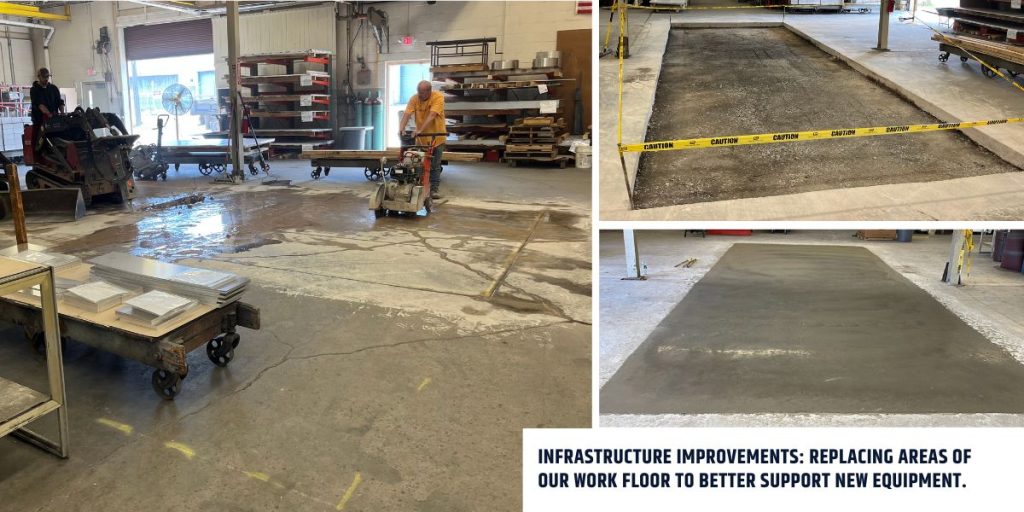
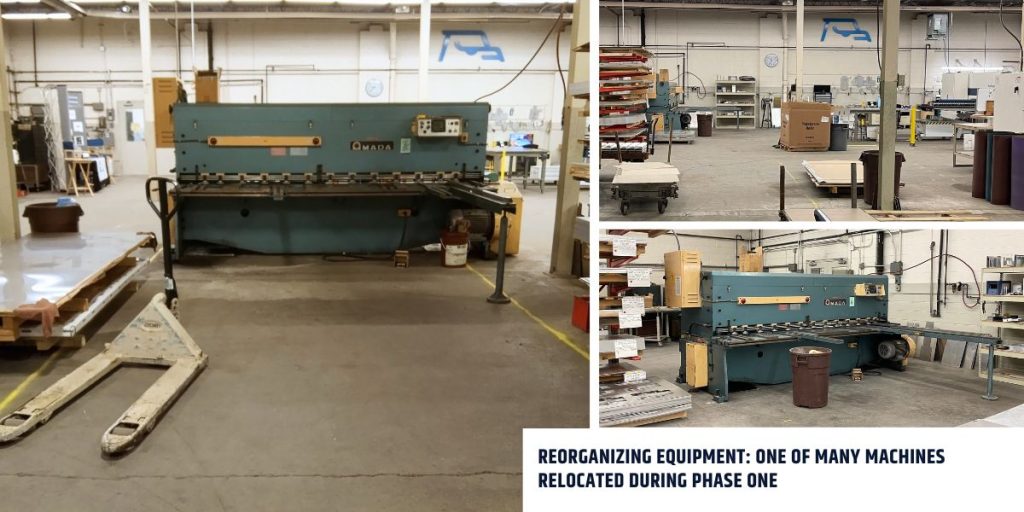
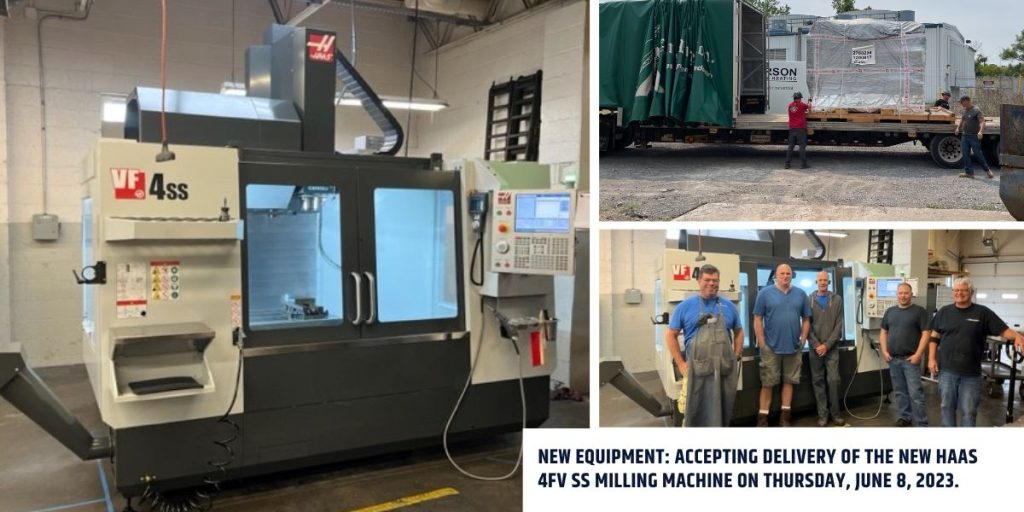
Phase 2 of our Capital Project taking place this month also includes:
- Moving our TIG welding area
- Moving Spot Welding Machines
- Moving raw material storage
- New LVD 6 Kw laser delivery
In October, we will roll out Phase 3, moving the old laser out, moving the shipping receiving area, and implementing new layouts for the powder coating department.
“Safety, Quality, Delivery, and Cost Competitiveness are the main drivers for these improvements,” Michael said. “We have wonderful customers, and they hold us accountable for driving these four categories to help them stay competitive as well. It’s a win-win for all of us.”
Michael purchased Eagle Metalcraft from the Helmer Family in 2022 and has since made strategic improvements to the company as it celebrates its 70th anniversary in business. This includes becoming a certified Veteran Owned Small Business, opening up Eagle Metalcraft’s contract opportunities. Additionally, Michael was named the 2023 Veteran Owned Small Business Entrepreneur of the Year for upstate New York.
Making the Factory Floor More Efficient
Improving the layout of our factory floor achieves numerous long-term goals for Eagle Metalcraft, including:
Increased Productivity
Efficiency improvements lead to increased production output without necessarily increasing the number of resources or time invested. By optimizing processes, streamlining workflows, and reducing waste, we can produce more goods within the same timeframe, resulting in higher productivity levels.
Cost Reduction
Improved efficiency often translates to cost savings. By eliminating waste, reducing downtime, and optimizing resource allocation, Eagle Metalcraft can lower operational expenses. This will include savings on energy consumption, raw material usage, and maintenance expenses, among others.
Enhanced Competitiveness
In today’s global marketplace, competition is fierce. By making the factory floor more efficient, we will gain a competitive edge, delivering products to market faster, responding to customer demands more swiftly, and offering more competitive pricing due to reduced costs.
Quality Improvement
Efficiency improvements can also lead to better product quality. By optimizing production processes and minimizing errors or defects, Eagle Metalcraft will enhance the consistency and reliability of our products. This, in turn, will improve customer satisfaction, brand reputation and reduce the need for rework or returns.
Scalability and Flexibility
An efficient factory floor is better equipped to handle increased production demands or changes in product lines. By optimizing workflows and ensuring resource utilization is efficient, we will scale up or down operations more easily. This agility allows us to respond quickly to market fluctuations, customer preferences, and new opportunities, specifically considering our newly acquired SDVOSB certification.
Employee Satisfaction and Safety
Efficiency improvements will positively impact our team members by creating a safer and more comfortable working environment. Streamlined processes can reduce physical strain, minimize repetitive tasks, and enhance ergonomics. Moreover, by eliminating bottlenecks and optimizing workflows, our staff can work more efficiently and experience increased job satisfaction.
Environmental Sustainability
Here at Eagle Metalcraft, we are increasingly conscious of our environmental impact. Making our factory floor more efficient will reduce energy consumption, minimize waste generation, and optimize the use of resources. This benefits the environment and aligns with the growing consumer demand for sustainable practices.
“Overall, improving factory floor efficiency is a strategic decision that will yield numerous benefits,” Michael said.
Above all, Michael is grateful that his team members have accepted all the changes implemented since he acquired the business.
“Change is tough, and our team has been taking this all in the spirit to do more for our customers and each other,” he said. “Everything we do is based around our wonderful team members and growing each other.”